Pumps in Motion: The Key to Efficient Industrial Fluid Handling
In the intricate world of industrial operations, the handling of fluids plays a pivotal role. Whether it’s water, oil, chemicals, or any other liquid, the efficient and safe transportation of these substances is essential. This is where industrial pumps come into play, serving as the backbone of fluid handling in various sectors. This article will explore the importance, types, innovations, and future trends in industrial pump technology.
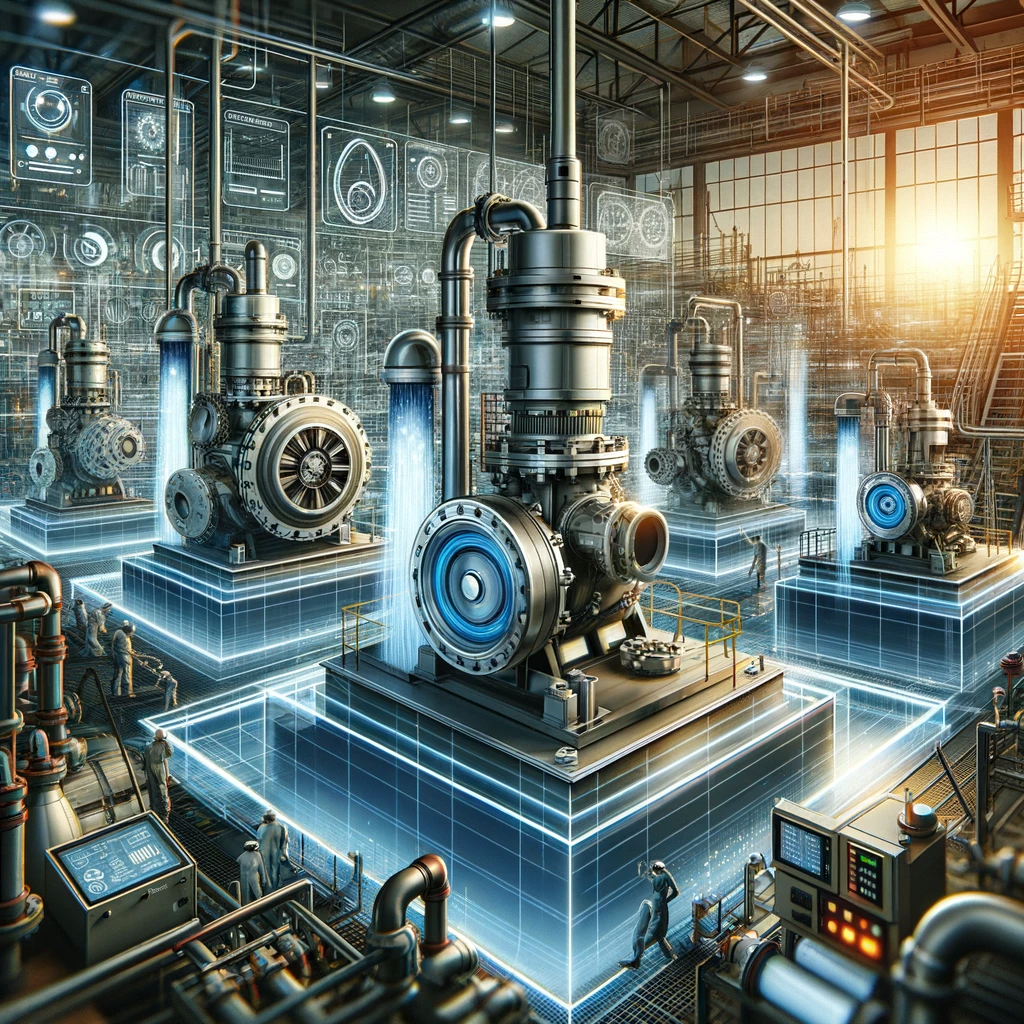
The Critical Role of Industrial Pumps
Industrial pumps are vital in numerous applications across various sectors, including oil and gas, chemical processing, water treatment, and manufacturing. These pumps are designed to move fluids efficiently and reliably, often under challenging conditions. They are not just about moving liquids from one place to another; they play a crucial role in ensuring the quality, safety, and efficiency of industrial operations.
Types of Industrial Pumps and Their Applications
There are several types of industrial pumps, each suited to specific tasks and fluids. Some of the most common include:
- Centrifugal Pumps: Widely used in many industries due to their versatility and efficiency in moving large volumes of liquid.
- Positive Displacement Pumps: Ideal for handling viscous fluids or fluids containing suspended solids.
- Diaphragm Pumps: Often used in the chemical industry due to their ability to handle aggressive or corrosive fluids.
Each type has its unique mechanism and suitability for different applications, making the choice of pump critical for operational efficiency.
Technological Advancements in Pump Design
Recent years have seen significant advancements in pump technology. Modern pumps are not only more efficient but also smarter. Innovations include:
- Energy-Efficient Motors: Reducing power consumption while maintaining high performance.
- Smart Pumps: Equipped with sensors and IoT technology, these pumps provide real-time data on performance and maintenance needs.
- Material Advances: New materials that resist wear and corrosion, extending the lifespan of the pumps.
These technological advancements are crucial in an era where energy efficiency and sustainability are paramount.
The Role of Pumps in Energy Efficiency
One of the significant benefits of modern industrial pumps is their contribution to energy efficiency. Since pumps are often one of the largest energy consumers in industrial processes, improvements in pump efficiency can lead to substantial energy savings. This not only reduces operating costs but also minimizes the environmental impact of industrial operations.
Case Studies: Successful Implementations
Real-world examples abound where innovative pump solutions have transformed operations. For instance, in the water treatment industry, advanced centrifugal pumps have dramatically reduced energy consumption while increasing water flow rates. In the chemical industry, specialized diaphragm pumps have improved the safety and efficiency of handling hazardous materials.
Future Trends in Pump Technology
Looking to the future, the trend is towards even more efficient and intelligent pumps. Predictive maintenance, powered by AI and machine learning, is expected to become standard, enabling preemptive repairs and reducing downtime. Additionally, further advances in eco-friendly materials and renewable energy-powered pumps are anticipated.
Conclusion
Industrial pumps are the unsung heroes of fluid handling in various industries. They are crucial for operational efficiency, safety, and environmental sustainability. As technology continues to advance, we can expect industrial pumps to become even more efficient, intelligent, and integral to industrial processes.